The impact advanced technologies has on manufacturing operations will continue to grow. Getting ahead of these technologies will ensure organizations stay competitive.
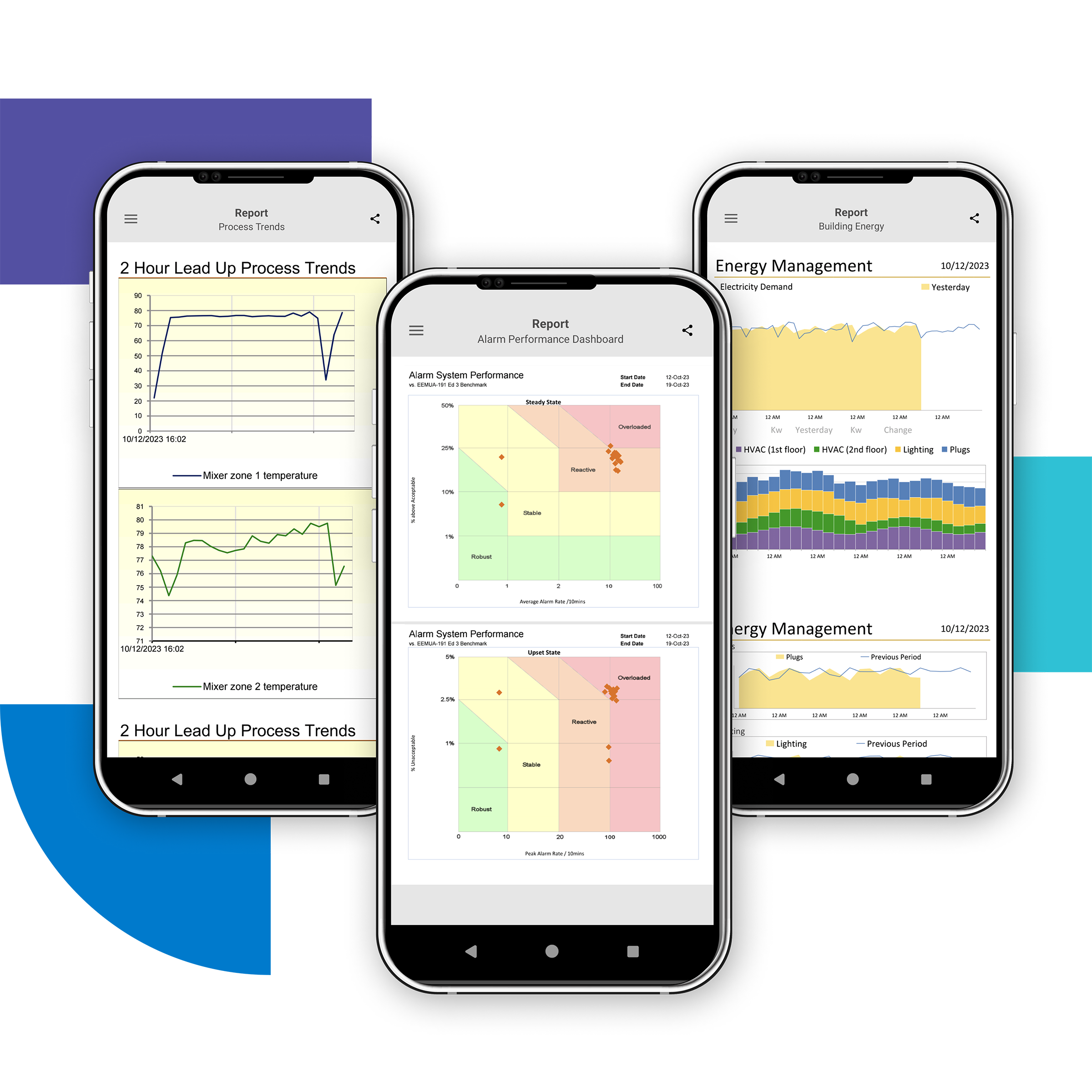
AI in manufacturing insights
- Most companies that intend to implement automation into their plants in the next 12 months intend to do so to increase product quality.
- Real-time data provides immediate insights into bottlenecks, inefficiencies and potential breakdowns for quick adjustments to maintain optimal performance.
- Integrating additional software accelerates digital transformation with advanced data collection for overall equipment effectiveness (OEE) and Manufacturing Execution Systems (MES).
The impact advanced technology has on manufacturing is undeniable. A responsible investment in technology can go a long way to meeting strategic long-term goals. New technologies like artificial intelligence (AI) can help companies streamline their processes, improve efficiency and reduce costs. Technology can also help companies stay ahead of their competitors by providing the needed tools to innovate and adapt to changing market conditions.
Digital technology and interconnectivity are driving influential technologies like advanced computing solutions; cloud and remote computing; Internet of Things (IoT) and connected devices; smart and real-time data sensors; data capture, software analytics and processing; and the adoption of AI and machine learning. To remain competitive — particularly considering worker shortages and increase productivity demands — Industry 4.0 and its complementary technology must be embraced.
Nearly two-thirds of chief financial officers reported that their companies have a strategic priority to automate tasks typically performed by employees, according to the 2024 CFO Survey, a collaboration between Duke University’s Fuqua School of Business and the Federal Reserve Banks of Richmond and Atlanta. Among firms that plan to automate in the next 12 months, the majority expect to implement AI to perform a wide range of tasks. Additionally, over the past year, nearly 60% of companies (and 84% of large companies) have implemented software, equipment or technology to automate tasks previously completed by employees. Here are the ways in which these companies intend to use automation.
- Substitute for workers: 33%
- Reduce labor costs: 47%
- Increase production: 49%
- Increase product quality: 58%
Continuous operational improvement starts with capturing data from machine assets. This data provides immediate insights for both people and systems, enabling them to make better, faster decisions and drive automation.
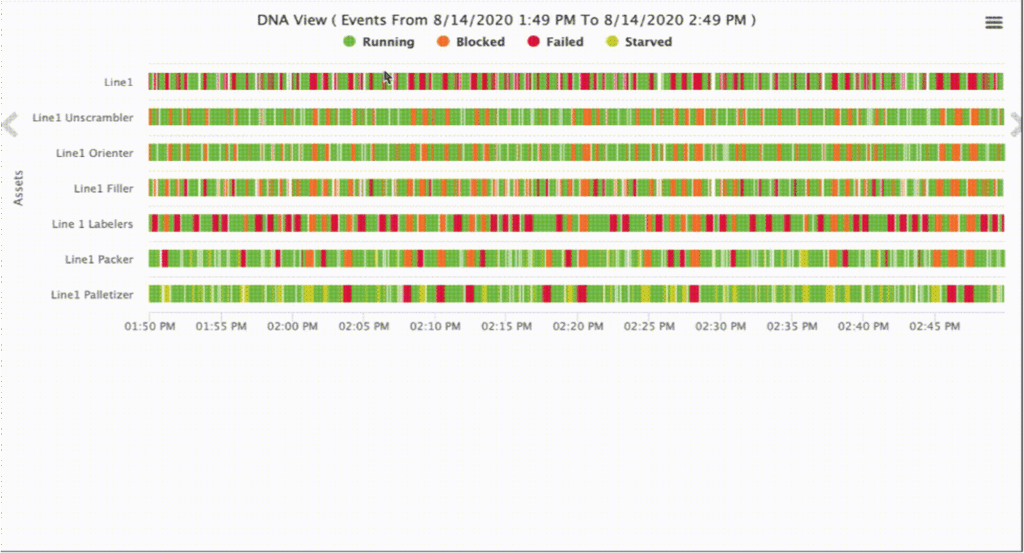
How automation is integrating data and manufacturing
Characterized by increasing automation and the employment of smart machines and smart factories, informed data helps produce goods more efficiently across the value chain. By collecting additional data from the factory floor and combining that with other enterprise operational data, a smart factory can achieve information transparency and better decisions. Accurate, real-time production data is pivotal to shop floor operations and the effective operation of each machine asset.
The use of data and analytics underpins Industry 4.0. Gathering, analyzing and sharing data across the enterprise is the entry point to leverage manufacturing technology to create more value. The added benefits include improved productivity, decreased production costs, better resource management and more profitability.
One of the primary advantages of data analytics in manufacturing is the ability to access real-time data. By leveraging this data, companies can monitor every aspect of their operations — from machinery performance to supply chain logistics — in real-time. This real-time data provides immediate insights into bottlenecks, inefficiencies and potential breakdowns, allowing for quick adjustments to maintain optimal performance. Additionally, they can implement improvements that enhance overall quality.
While accurate, real-time data is pivotal to operations, harnessing this data effectively requires advanced technology and analytical capabilities. Vast amounts of data are collected for industry reporting, predictive maintenance and safety enhancements, for example, but manufacturers may be challenged to effectively manage and analyze the data. Analyzing historical data allows operations management to identify patterns, trends and anomalies that may otherwise go unnoticed. Historical data analytics can help companies transition from reactive to proactive planning and aligning with operations.
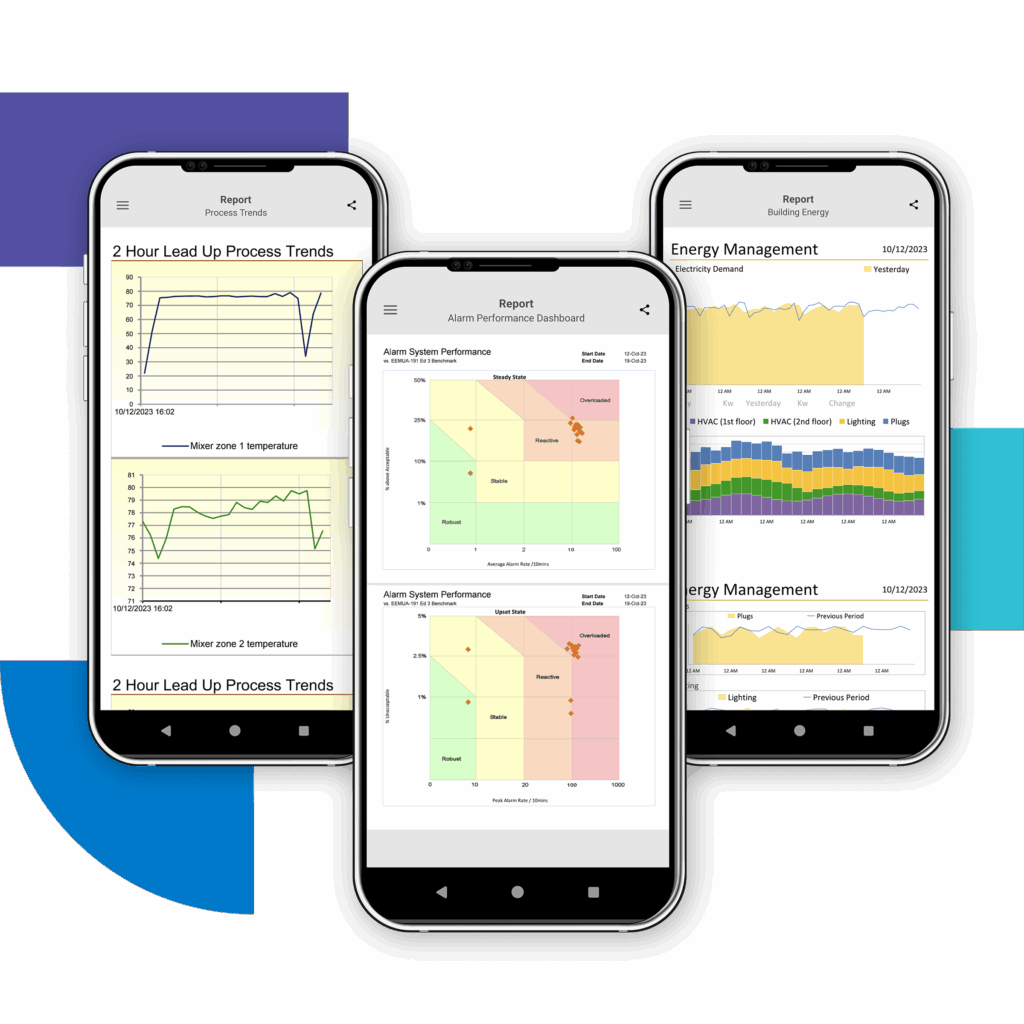
Using AI for reporting
Reports provide a visualization of this historized process information and correlate related process variables, compute metrics on that data and visually graph such data for easier pattern and anomaly detection. These reports are created through third-party software that seamlessly integrates with programmable logic controllers (PLCs), Supervisory Control and Data Acquisition (SCADA) and historian systems. Advanced reporting solutions can even pull information from remote alarm notification software, allowing further analysis and optimization of condition response times.
Reporting software enables organizations to turn raw process data into actionable information, thereby increasing efficiency and reducing costs. Furthermore, automated reporting solutions streamline regulatory compliance by collecting data from various sources like SCADA, Laboratory Information Management System (LIMS), manual entry and others. As the data is collected, it is summarized as key metrics — flow totals or turbidity threshold analysis. The final output is published into a formatted document accepted by regulatory agencies.
Integrating Manufacturing Execution Systems and AI
Advanced Manufacturing Execution Systems (MES) capture data directly from machines and operators to deliver real-time production metrics and analytics in easily usable formats.
Integrating additional software accelerates digital transformation with advanced data collection for overall equipment effectiveness (OEE) and MES, enabling plant personnel to have valuable insights into the operations and helping them make better and more informed decisions.
A PwC report emphasizes that data integration is among the top challenges faced during the implementation of Industry 4.0 initiatives, including MES adoption. However, effective data collection requires embracing advanced solutions that go beyond traditional methodology. A contemporary approach allows companies to feed data into level 3 to 5 systems — going beyond traditional bottleneck analysis.
Additionally, there are low-code and no-code technologies that eliminate problems with PLC data collection and can identify related alarms for richer analysis. This approach examines data from the production line and delivers intelligent root-cause analysis when issues arise, correlating event and alarm data to address upcoming production issues.
By deploying third-party advanced software, manufacturing plants can accelerate and drive OEE uplift, avoid problems before they occur and reduce engineering downtime by up to 70%. For a $1 billion company, every 1% improvement in OEE — like integrating advanced software that reduces equipment downtime — is worth approximately $7 million annually, further lessening costs and improving operational efficiencies.
As the industry continues to move toward greater efficiency, the integration of AI in MES is revolutionizing how manufacturers operate, bringing unprecedented levels of automation, predictive analytics and decision-making. AI-powered MES are driving innovation by enabling smarter factories, optimizing production cycles, reducing downtime and helping manufacturers achieve higher levels of productivity. According to a McKinsey report, the technology is expected to herald a new age of efficiency in operations: in manufacturing and supply chain alone it could reduce expenses by up to half a trillion dollars. AI can leverage root cause analysis to predict failures and reduce defects; draft easy-to-follow dynamic work instructions; and augment operator stations by offering live, AI-supported troubleshooting and operating guidelines, helping companies be more flexible, efficient and intuitive in meeting end-users’ needs.
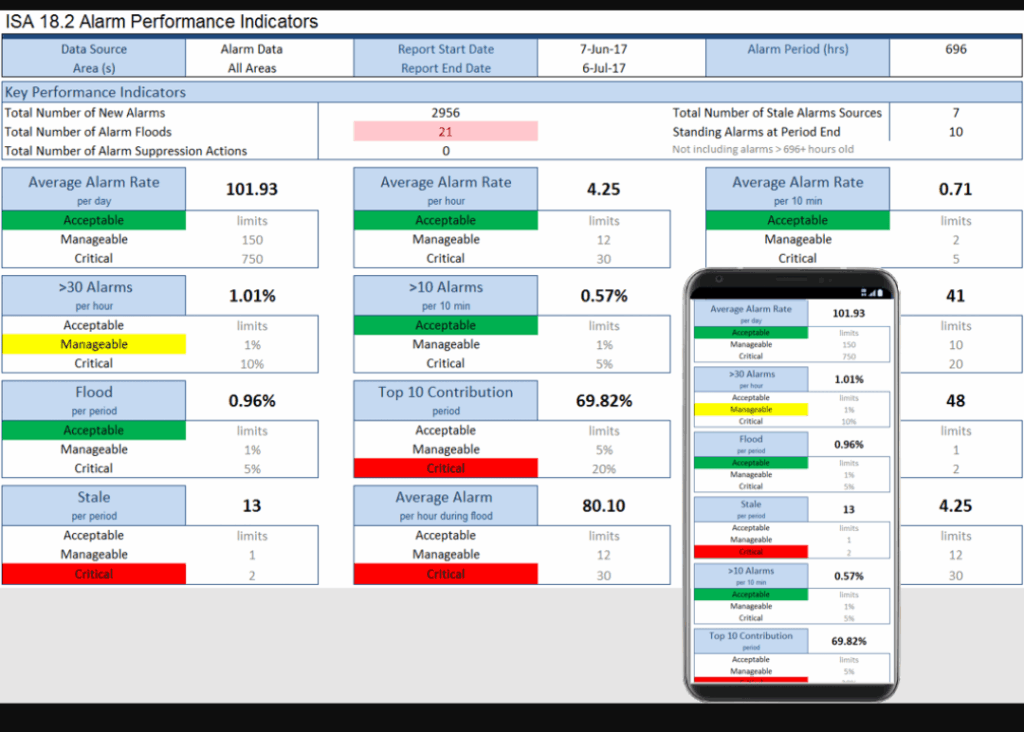
Ways Industry 4.0, IIoT and AI reshape industries
Industry 4.0, Industrial Internet of Things (IIoT) and AI are reshaping industries. Trying to meet these challenges with manually intensive processes and outdated technology is difficult. However, by leveraging advanced technology like cutting-edge software solutions, organizations can increase productivity and efficiency and reduce costs. Prioritizing operational excellence not only fosters growth but also positions organizations for continued success in an ever-evolving business and manufacturing landscape.
Cody P. Bann is the vice president of engineering and David Nolan is the industry solutions manager at SmartSights. Edited by Sheri Kasprzak, managing editor of Automation & Controls, WTWH Media, [email protected].