Industry 4.0 principles continue to transform manufacturing processes with comprehensive data integration, advanced analytics and artificial intelligence, easing operational challenges and regulatory compliance.
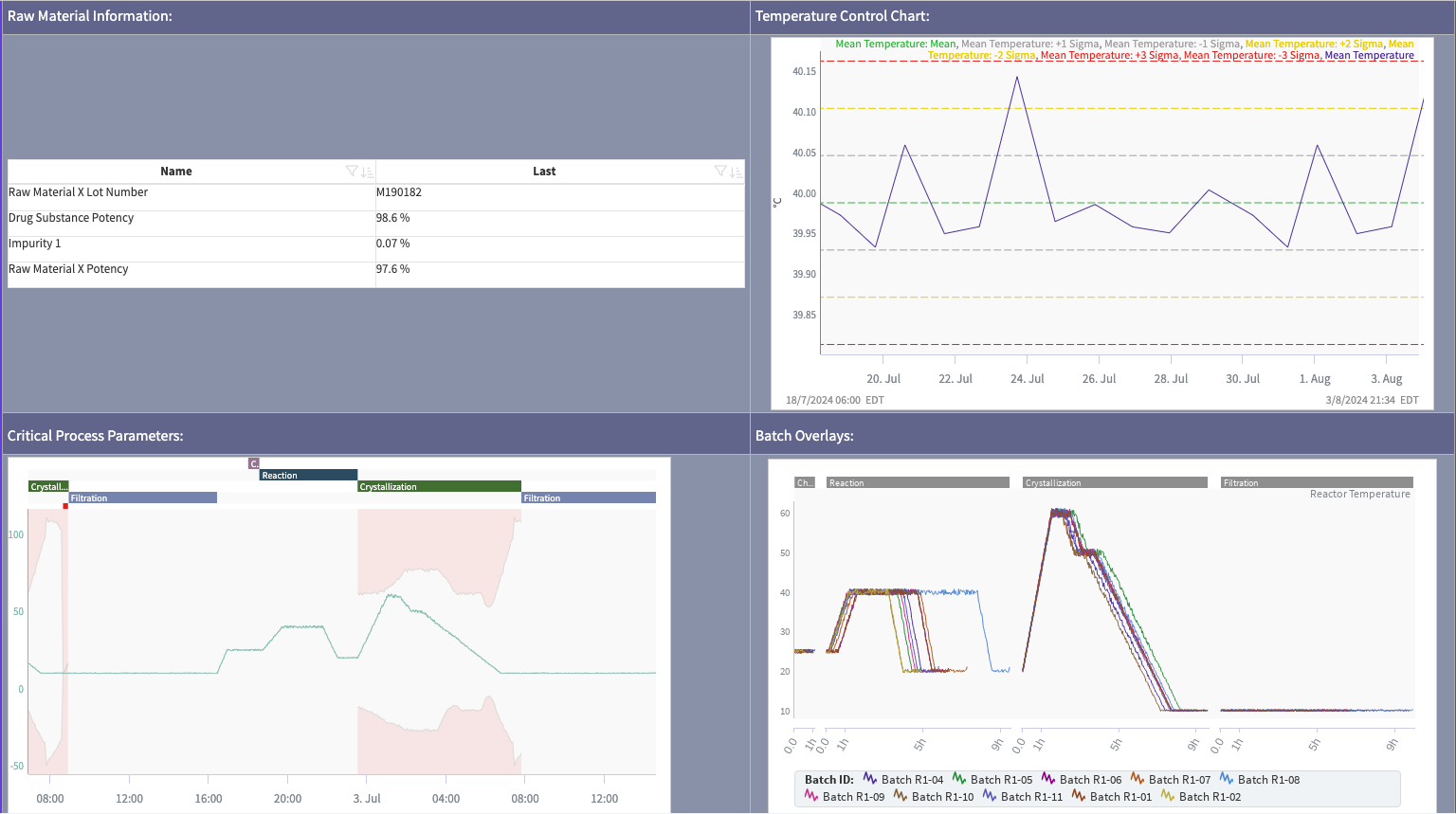
Industry 4.0 insights
- Managing the relationship between time-series and discrete data is critical in Industry 4.0, as it must all be consolidated and integrated to perform meaningful analysis.
- Vendor-agnostic advanced analytics platforms support real-time connectivity to numerous data sources, providing invaluable aggregation and contextualization for subject matter experts (SMEs).
- AI-driven tools have led to analyst agents capable of producing insights, identifying and comparing trends and generating reports.
At its core, Industry 4.0 — commonly used synonymously with smart manufacturing or smart factories — is based on the concept of cyber-physical system integration. This effort aims to control manufacturing processes using a combination of cyber and physical sensors and signals in myriad industries.
Industry 4.0 adoption is occurring at varying rates based on sector. While digital transformation is accelerating across the board, Digitopia reports a widening divide between digital pioneers and those hesitant to innovate, as many companies prioritize endurance and reliability over transformation, especially in risk-averse environments, such as pharmaceutical manufacturing.
For example, the International Society of Pharmaceutical Engineering (ISPE) suggests that the Industry 4.0 revolution in life sciences is likely to resemble more of an evolution due to the sector’s intricate product portfolios, lengthy development cycles and stringent regulatory requirements.
Regardless of the pace, the fundamental goal of adopting Industry 4.0 practices is enhancing industrial process understanding by leveraging the increased availability and accessibility of data. As sensors, control systems and automation technologies grow in quantity and generate increasingly vast amounts of data, driving meaningful outcomes by storing, accessing and processing this information effectively becomes ever more challenging.
Bridging the gap from data generation and management to actionable insights — moving from the cyber to the physical world — remains one of the most critical aspects of industrial digital transformation. Data analytics plays a key role in the shift, transforming raw data into valuable knowledge and some of the most groundbreaking innovations are occurring in this area.
Wrangling multiple data types from various sources
An organization does not become digitally mature overnight. As previously mentioned, it is an ongoing evolution that can often be slowed by inherent complexities and regulatory constraints, especially in more risk-averse process industries. Additionally, digital transformation rarely begins with a clean slate, as companies evolve through greenfield and brownfield expansions, acquisitions, mergers, partnerships and divestments.
All this activity can create fragmented data landscapes consisting of multiple incompatible technologies, platforms, solutions and standards. These often manifest in various process historians, data warehouses, data lakes and other sources, both on-premises and in the cloud.
Effectively managing the relationship between time-series and discrete data — such as online process signals and laboratory information management system (LIMS) data — is also critical, as it must all be consolidated and integrated to perform meaningful analysis. While IT consolidation projects can prove valuable, they come with cost and risk. For these and other reasons, it is essential for process manufacturers to standardize data integration using a commercial advanced analytics platform that seamlessly connects to each of their data sources.
Revisiting the pharma example, drug manufacturers must ensure consistent yield and process robustness across different lines and sites. This typically requires working with data stored in process historians, LIMS and manufacturing execution systems (MES) from multiple vendors, each with their own formats for storing data. Vendor-agnostic advanced analytics platforms, such as Seeq, support real-time connectivity to numerous data sources, providing invaluable aggregation and contextualization for subject matter experts (SMEs). However, data access is just the first step in the Industry 4.0 journey. Effective advanced analytics, calculations and reporting capabilities are necessary to deliver actionable insights to all data consumers within an organization (Figure 1).
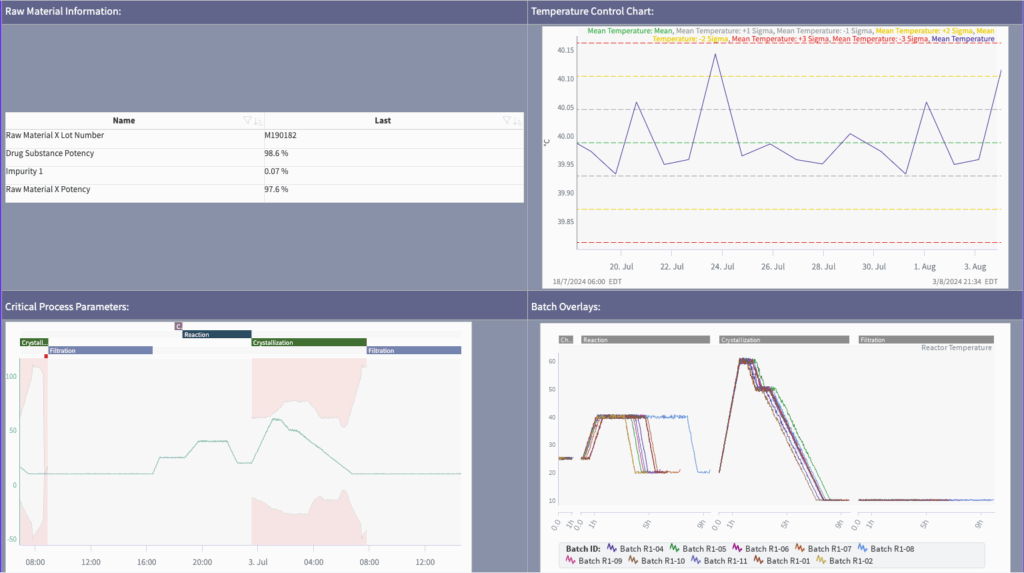
Contextualization and the path to knowledge
The ability to access manufacturing process signals alongside discrete data from MES, LIMS and other sources is required to add context to data — without which meaningful analysis would be impossible. Modern industrial analytics solutions must go beyond static asset and event frame definitions, enabling the combination of multiple conditions and logic for more dynamic insights.
For instance, Merck, a multinational pharmaceutical manufacturer, recently introduced its next-generation operational availability/overall equipment effectiveness (OA/OEE) digital tool for finished dosage forms manufacturing. This solution integrates process, MES and plant scheduling data with flexible and scalable calculations to generate real-time visualizations tailored to different user roles, ranging from shop floor operators to engineers and managers.
The key to the OA/OEE tool’s success lies in seamless data connectivity, advanced analytics and robust reporting capabilities, all working together to deliver real-time and actionable insights that drive quick interventions and continuous improvement. This approach fosters significant gains in production capacity.
Smart alarm management
Preventing deviations before they occur is a top priority in the process industries, as quality events can trigger significant batch losses and lengthy, costly investigations. While the use of alarms in plant automation systems is a long-established element of identifying offspec product, control systems are increasingly implementing additional real-time asset and process monitoring for advanced condition detection. This often consists of soft alarms and other means of detecting operational anomalies that, if not addressed, can lead to process failures or out-of-compliance product. These early warnings provide SMEs with ample time to implement corrective actions before issues escalate.
However, in the event processes begin to deviate, managing numerous alerts quickly causes alarm fatigue. Furthermore, when false positives trigger additional alerts, alarms can increasingly become noise, which is easily ignored. However, advanced analytics platforms provide more efficient means of managing and interpreting alarms.
For example, engineers at pharmaceutical giant, Lilly, developed a smart alert management solution for asset monitoring that integrated process data with alerts to provide contextualized operational insights. By monitoring real-time alert duration within a given batch and performing statistical process control calculations against historical performance, the team filtered out noise, highlighting only critical issues. This provided timely and actionable insights for operators, reducing average intervention time from days to mere minutes or hours. This shifted line performance analysis from scheduled, after-the-fact reviews to continuous, real-time monitoring.
Improving SME workflows with AI-aided advanced analytics
Interest in artificial intelligence (AI) is also booming throughout all industry segments. However, while the potential is immense, early AI solutions often failed to deliver on ambitious promises, leading to a cautious response, especially in heavily regulated industries where guidelines remained unclear.
In time-series data analytics, AI can serve as an assistant, amplifying SME workflows to boost productivity and accelerate time to insight. For AI to be most effective, both SMEs and AI tools require high-quality data, contextual information and a flexible platform that supports implementation and operationalization. AI in this context does not replace, but rather complements, SMEs and advanced analytics platforms.
Advanced analytics applications remain essential for deriving insights from data, as they centralize information from disparate sources, simplify access, establish context and enable live updates. AI provides value both as a user interface and as a decision-support tool, but context is critical for accuracy and effectiveness in analytics workflows.
Even the most user-friendly data analytics platforms require time to master, although AI assistants can dramatically shorten time to proficiency by guiding users, explaining functionalities and performing analyses based on natural language prompts (Figure 2).
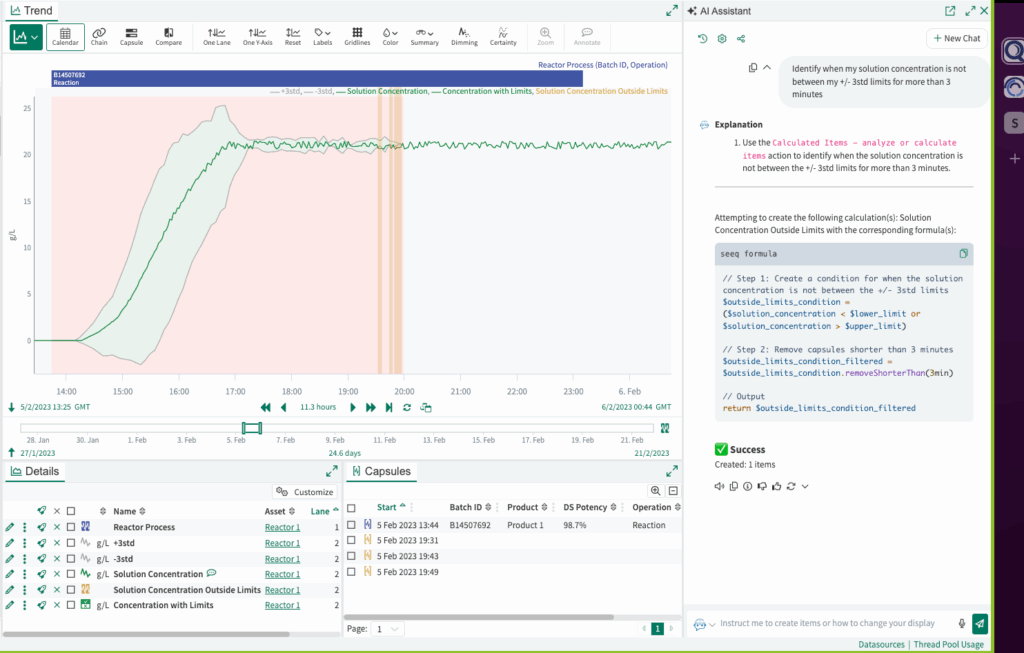
Recent developments have led to analyst agents capable of producing insights, identifying and comparing trends and generating reports. These AI-driven tools provide invaluable support and second opinions for SMEs, rendering them an increasingly essential component of operational optimization.
Digital transformation continues
Digital transformation in the process industries is steadily progressing across the board. While Industry 4.0 promises greater efficiency, quality and process optimization, realizing these benefits requires overcoming significant challenges, including fragmented data landscapes and regulatory uncertainty. Furthermore, digital transformation can be more evolutionary than revolutionary in heavily scrutinized industries due to inherent complexities and compliance constraints.
Consolidating and contextualizing data from multiple sources is a critical enabler for digital maturity and advanced analytics platforms with AI-powered tools play a pivotal role in this transformation. These platforms facilitate real-time insights, improve alarm management and enhance subject matter experts’ workflows, helping accelerate problem-solving and shift operational analysis from reactive and scheduled reviews to continuous and proactive monitoring. As AI capabilities continue to evolve, their role in industrial analytics will expand, providing SMEs with more intuitive interfaces, predictive insights and automated decision-support systems.
The Industry 4.0 journey is not simply about adopting new technologies, but fostering data-centric cultures that embrace innovation while maintaining required regulatory standards. Companies that strategically invest in advanced analytics, AI and data integration solutions position themselves advantageously to bridge the digital maturity gap, drive continuous improvement and unlock new levels of operational excellence.