Machine vision applied to inspection applications is enabled by artificial intelligence (AI) to new levels of quality and efficiency on the plant floor. See five considerations for implementing AI vision inspection.
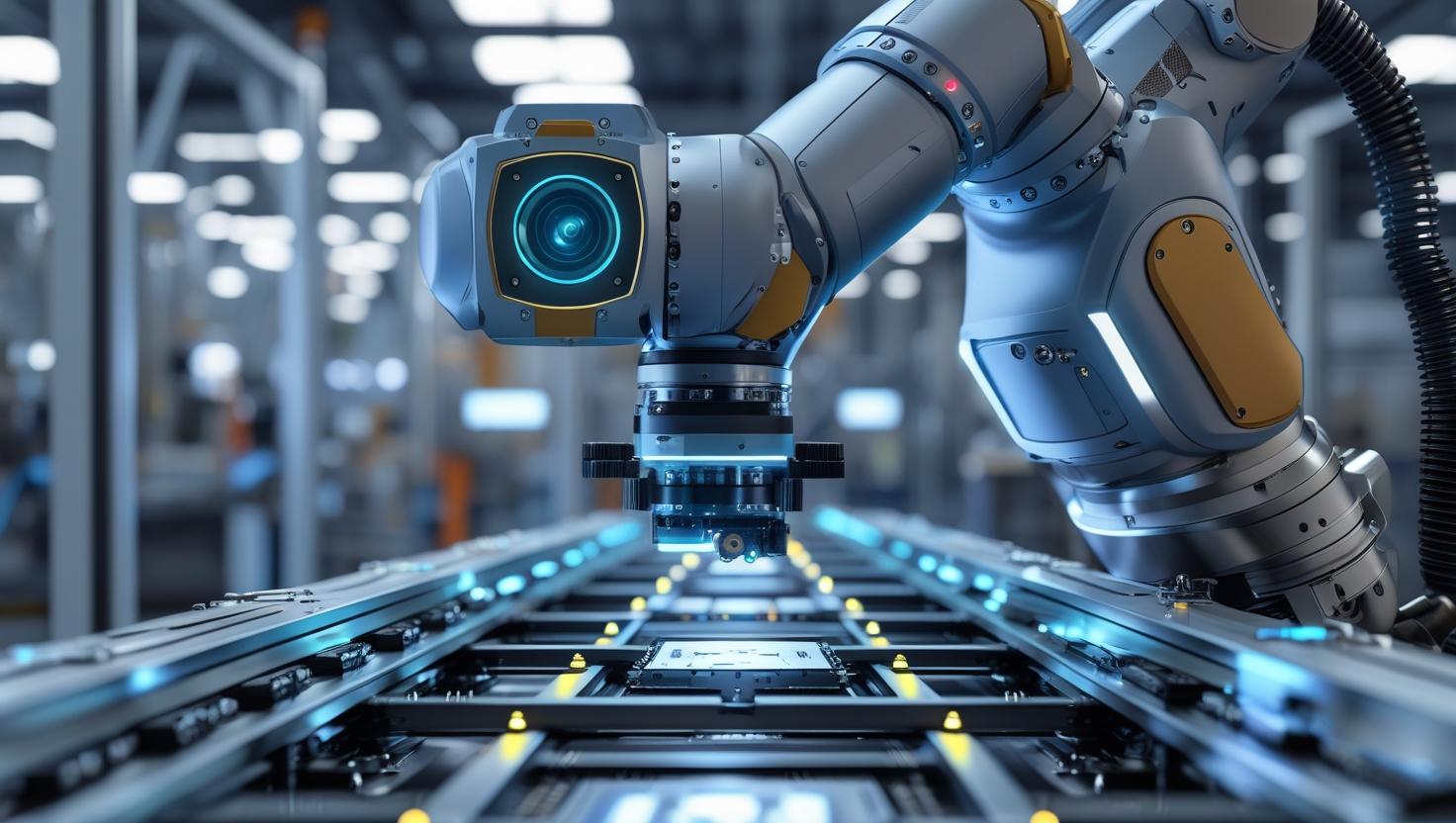
AI vision inspection insights
- AI-powered vision inspection helps overcome the limitations of legacy vision systems in dynamic production environments.
- Contextualized defect data and real-time analytics can accelerate root cause analysis and improve production efficiency.
- There are key implementation strategies for AI vision systems.
Artificial intelligence (AI)-powered vision inspection is helping manufacturers improve quality, reduce waste and adapt quickly to product changes. By enabling real-time defect detection, root cause analysis, and scalable model updates, machine vision systems enabled by AI are driving new levels of efficiency on the plant floor.
In fast-paced, high-stakes production environments, quality and throughput are nonnegotiable. For decades, manufacturers have relied on machine vision to identify issues like missing components, misaligned labels, or damaged packaging before products reach customers. As operations grow more complex, with greater product variability, faster changeovers and increased pressure on margins, traditional vision systems are hitting their limits. Rigid rules-based logic, siloed data and the need for constant manual intervention make legacy vision systems difficult to scale, adapt and maintain.
Quality has emerged as a priority in smart manufacturing initiatives. Nearly half of industry leaders plan to use AI and machine learning to up-level and strengthen quality control, signaling a clear shift from legacy rigid rule-based tools to flexible AI and machine learning solutions to keep pace with modern production demands.
AI vision inspection is reshaping modern manufacturing by enabling earlier detect defection, faster root causes analysis and real-time, actionable insights that boost efficiency, reduce waste and support continuous improvement across the production line.
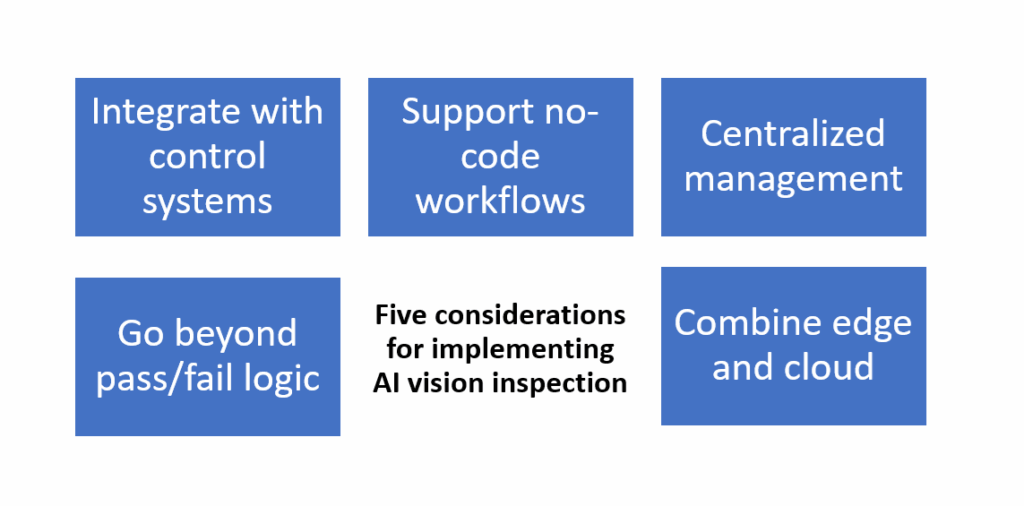
Limits of traditional machine vision systems
Conventional vision systems are typically programmed for a narrow task, often optimized for one inspection use case. Updating these systems to support new product variants or packaging changes often requires onsite engineering work, software reconfiguration and/or system downtime. This rigidity creates bottlenecks and quality blind spots in dynamic production environments.
Equally problematic is the limited data output. Most systems offer little more than binary pass/fail signal, leaving quality teams with unanswered questions: Why did this defect happen? Is it part of a pattern? What should change upstream to prevent it?
As a result, many manufacturers may limit the project scope of the vision system to sample product quality instead of full-scale, 100 percent part inspection across multiple lines or facilities, especially when the cost or complexity of system updates becomes prohibitive.
In a high-speed consumer goods facility, where conveyor speeds can reach up to 1200 parts per minute, hundreds of misclassified or undetected flaws may escape into the supply chain or false rejects are ejected from the production line. In highly regulated industries, like consumer goods, even minor quality issues can pose serious safety risks.
A smarter approach to machine vision with AI vision inspection
AI-powered vision inspection systems overcome these challenges by combining intelligent defect detection with context rich analytics. Unlike rigid rule-based vision systems that provide binary pass or fail signals, AI systems can classify defect types that may appear inconsistent in appearance and location, providing real-time contextualized insights pointing to root cause that may be acted on by operators and quality teams enabling data driven business decisions to optimize operations.
AI systems are inherently more adaptable. Cloud-based training and model management allow updates to be deployed across lines and facilities without physical intervention. Larger datasets that capture example images representing part to part variation enable AI models to be refined through continuous learning, increasing model flexibility to deal with increased application subjectivity without training from scratch.
Most importantly, AI vision platforms are designed to democratize and provide easy access to advanced vision capabilities without requiring prior knowledge or experience. With intuitive interfaces and no code tools, plant floor teams can label images, train models and adjust inspection parameters without programming expertise. This empowers plant-floor personnel who are closest to the process to drive quality improvements directly.
Five considerations for implementing AI vision inspection
To take full advantage of AI vision inspection, manufacturers should prioritize the following:
- Go beyond pass/fail logic: Choose platforms that provide defect classification and trend analytics to enable root cause analysis and targeted improvements.
- Centralized management: Use platforms with unified dashboards to monitor and configure inspections remotely across multiple lines and plants.
- Support no-code workflows: Empower front-line teams to configure inspection parameters for new products or processes with no coding required.
- Integrate with control systems: Ensure seamless connectivity to programmable logic controller (PLC), manufacturing execution system (MES) or enterprise resource planning (ERP) platforms to support real-time actions like reject handling or alerts.
- Combine edge and cloud: Leverage edge computing for real-time inference while using cloud-based learning for continuous model refinement and enterprise-wide scalability and insight.
The payoff: Continuous plant-floor quality and operational gains
Manufacturers adopting AI vision are seeing measurable improvements. Richer, contextualized defect detection data accelerates root cause analysis, while flexible AI models enable fast adaptation to new products, packaging designs or materials. By detecting and correcting issues earlier in the process, often before products leave the line, waste and rework is reduced and production yield increased.
AI vision inspection is more than a quality assurance tool; it’s a strategic enabler of digital transformation giving manufacturers the insight, agility and control needed to maintain consistent, high-quality production in an increasingly complex interconnected production landscape at scale.
Carl Lewis is senior product manager, Rockwell Automation. Edited by Mark T. Hoske, editor-in-chief, Control Engineering, WTWH Media, [email protected].
CONSIDER THIS
Are you implementing modern AI-enabled machine vision in all appropriate ways?
ONLINE
More on machine vision is available from Control Engineering.